Understanding Gas Detectors: A Comprehensive Guide to Safety and Technology
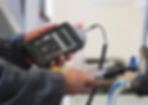
Gas detectors are vital safety tools used across numerous industries to detect the presence of harmful gases in the environment. Whether it’s a confined workspace, a residential building, or a chemical plant, gas detectors serve as early warning systems to prevent life-threatening accidents. As the world continues to prioritize safety and environmental consciousness, gas detection technology is becoming more advanced, reliable, and widely used.
This blog explores the fundamentals of gas detectors, including how they work, their types, uses, technological innovations, and the importance of proper maintenance and calibration.
🔍 What is a Gas Detector?
A gas detector is a device that identifies the presence of gases in an area, often as part of a safety system. It’s designed to detect toxic, combustible, or asphyxiant gases and alert users through visual, audible, or vibrating alarms. These detectors are crucial in workplaces where hazardous gases might be present due to industrial processes or equipment malfunctions.
Some gas detectors are fixed and continuously monitor an area, while others are portable, allowing for on-the-spot testing and flexibility in movement.
🛠 How Gas Detectors Work
Gas detectors use sensors to measure gas concentration. The type of sensor depends on the gas being detected and the required sensitivity. Here are some common sensor technologies used:
Catalytic Bead Sensors: Detect combustible gases by measuring the heat released during oxidation.
Electrochemical Sensors: Commonly used for detecting toxic gases like carbon monoxide and hydrogen sulfide.
Infrared Sensors: Detect hydrocarbons and CO₂ by measuring the absorption of infrared light.
Photoionization Detectors (PID): Ideal for detecting volatile organic compounds (VOCs).
When the concentration of a specific gas reaches a predefined threshold, the detector triggers an alarm to alert personnel.
🧪 Types of Gases Detected
Gas detectors are designed to sense various types of gases, such as:
Combustible gases (e.g., methane, propane)
Toxic gases (e.g., carbon monoxide, hydrogen sulfide, chlorine)
Asphyxiant gases (e.g., nitrogen, carbon dioxide)
Volatile organic compounds (VOCs)
Oxygen (deficiency or enrichment)
🏭 Applications and Industries Using Gas Detectors
Gas detectors are used in a wide range of environments, including:
Oil and Gas: Detect flammable and toxic gases to prevent explosions and protect workers.
Chemical Manufacturing: Monitor hazardous chemical leaks or spills.
Mining: Prevent the buildup of methane and monitor oxygen levels underground.
Construction: Check confined spaces like tunnels or tanks for harmful gases.
Firefighting and Rescue: Detect gases in emergency environments.
Residential Buildings: Monitor carbon monoxide leaks from gas appliances.
Laboratories and Research Facilities: Ensure controlled and safe environments when working with chemicals.
⚙️ Fixed vs. Portable Gas Detectors
Fixed Gas Detectors are permanently installed in facilities to provide continuous monitoring in specific locations. These systems are ideal for high-risk areas where gas leaks can occur regularly.
Portable Gas Detectors are handheld devices used for spot-checking or personal safety. They are often used by first responders, utility workers, and technicians entering confined spaces.
Both types are essential, depending on the environment and the type of monitoring required.
🚀 Technological Advancements in Gas Detection
Modern gas detectors are not just about sounding alarms — they integrate advanced technology for better accuracy, usability, and data management. Some key innovations include:
Wireless Connectivity: Gas detectors can transmit real-time data to remote monitoring systems.
Multi-Gas Detection: Devices that detect multiple gases at once are now common, improving efficiency and coverage.
Smart Sensors: Enhanced sensitivity, self-calibration features, and longer lifespans.
Data Logging and Analysis: Helps industries track exposure trends, conduct safety audits, and comply with regulations.
Mobile App Integration: Allow remote control and real-time alerts through smartphones.
These technological improvements have made gas detection more reliable and easier to integrate into comprehensive safety systems.
🔧 Importance of Calibration and Maintenance
Just like any other instrument, gas detectors must be regularly calibrated and maintained to ensure their accuracy. Calibration involves exposing the detector to a known concentration of gas to adjust its readings. Maintenance routines include:
Sensor inspection and replacement
Battery checks and replacements
Functional tests (bump tests)
Software updates (for digital models)
Neglecting these tasks can lead to false readings or device failure, which can be dangerous in critical environments.
📈 Why Gas Detectors Matter
The consequences of gas leaks or exposure to toxic gases can be catastrophic. From explosions and fires to long-term health effects or even fatalities, the risks are high. Gas detectors serve as a critical line of defense by providing real-time alerts and allowing timely intervention.
Moreover, they play a role in ensuring regulatory compliance. Governments and workplace safety agencies often mandate the use of gas detection systems in hazardous environments.